Gases have been a key enabler in the electronics industry since the advent of commercial transistors and integrated circuits in the mid-twentieth century. Gases have many unique properties, including: ease of transport and storage, ease of precise distribution, and most importantly, ease of controlling the desired chemical reactions at the molecular level. These properties make the gas ideal for building more complex electronic devices.
Electronics are built from semiconductor devices (capacitors, diodes, and transistors), and the latest computer chips are produced in more than 1,000 steps and contain more than 10 billion transistors, all connected by nanoscale wires in intricate 3D designs . These products are manufactured using the simplest building-block process, and most products are constructed and shaped using gaseous materials.
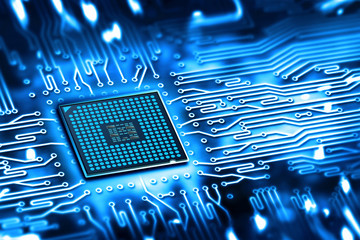
The 6 main processes and the required gases are described below
1. Electronic technology
Electronic devices are fabricated on initial substrates. The substrate is often used as the primary electrical insulator for the device. Sometimes the substrate may just be a temporary part that will be removed after fabrication. In addition to silicon wafers commonly used in semiconductor chips and solar cells, other materials such as sapphire, gallium arsenide and silicon carbide are also used to make power management chips and LEDs. Nearly all electronic processing involving gases takes place in metal-walled reactors or reaction chambers where process chemistry can be precisely controlled.
Typically, the reaction chamber is maintained at a low pressure level to eliminate atmospheric contamination from gas-phase chemical reactions and to remove remaining chemical reactants or products within the reaction chamber. Temperature control is also very important. The substrate is typically placed on a horizontal surface that can be heated or cooled to the desired temperature. Helium or other gases can flow over the surface to help with temperature control. The following are the main processes for making computer chips and some of the main gases used.
2. Deposition
Deposition is a production process that makes the materials inside electronic devices such as conductors, semiconductors, and insulators. Typically, the two gas-phase reactants flow into the reaction chamber, while the substrate is heated to a high temperature conducive to the desired reaction, so that a thin-film product can be formed directly on the surface of the upper layer. This reaction can be further activated by using argon or helium plasma.
Many different gases are used in the deposition step, which are used as precursors for thin film production. Some gases (such as ammonia and methane) have been used since the beginning of semiconductor manufacturing, others have been used later, and still others have been specially developed for use in electronics. Because more than 60 elements are used in the production of electronic devices, completely new gas-phase materials must be developed to support the development of manufacturing and design.
3. Photolithography
Lithography is the process of shaping the shape of a device and is critical to enabling the miniaturization of microchips. A lithography machine, called a scanner, is like a slide projector: it takes light from a light source to transmit the master image etched on the glass piece to a substrate covered with a photosensitive chemical film. The image is a pattern of the tiny circuits that form the microchip. The pattern is then wet-chemically developed and the exposed or unexposed portions of the chemical film are removed.
Importantly, the light sources commonly used in image lithography are based on gas-phase lasers, using small amounts of fluorine, chlorine, hydrogen chloride, argon, and xenon mixed with a large amount of neon as the balance gas. Photolithography is the most widely used process for neon gas. Carbon dioxide is also used as a processing aid to reduce defects in images. A new photolithography method will use an excited state of tin vapor to generate light. But because tin deposits on expensive optics, large amounts of hydrogen are used to react with tin to remove the tin as tin hydride (SnH4) through a vacuum system.
4. Etching
Etching is a process used to selectively remove material and is usually followed by photolithography to fix patterns and shapes formed in the photolithography process. The etching gas is activated in an argon plasma above the substrate and then reacts with a material on the surface. The reaction product is also a gas and can be vented through a vacuum system.
Most etching gases are carbon-based and contain fluorine or other halogen atoms. The composition of the fluorocarbon aids in the selection of the target film. When excited in the plasma, these activated gases are highly reactive towards the target material on the substrate surface. During fabrication, these fluorocarbon debris can also be deposited in other areas of the device and act as a protective layer. Oxygen is also sometimes used as a co-reactant.
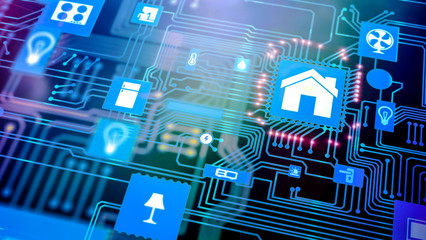
5. Doping
Doping is a process that helps change the conductivity of semiconductor materials. By adding atoms of these materials to a previously deposited semiconductor material, circuit engineers can determine the conditions under which the semiconductor layer conducts electrons. Doping atoms can be added by reacting gases at the surface and infiltrating the heat-treated substrate, or by plasma activation. During plasma activation, an electric field is used to speed up the doping of the substrate.
Gases used for doping include arsine (AsH3), phosphine (PH3), and boron-containing gases such as boron trifluoride (BF3) and diborane (B2H2). Arsine and phosphine, in particular, are highly toxic and are typically stored and used in safe dispensing containers, preventing leakage of these materials by limiting the effective pressure to below atmospheric pressure. Diborane is not thermally stable, decomposes slowly, and can be stored at refrigerated temperatures and mixed with hydrogen. Adding germanium to a thin film of silicon can alter its conductivity by slightly disrupting the silicon's crystal structure.
6. Annealing
Annealing is another process used to alter the composition of existing films. Oxygen or hydrogen is typically used at high pressure and temperature to react with existing layers of material to form new oxide or hydrogen layers on the surface. In other applications, substrates with more film layers are heated and cooled so that the top film can form a crystalline phase.
Argon is often used when making silicon ingots that can be cut into semiconductor and solar wafers. This is because nitrogen reacts with silicon at its melting temperature (1414°C).
Cleaning the reaction chamber is an important process to keep the reaction chamber in working condition. Excessive chemical reactants and products will not only deposit on the substrate, but also on the walls of the reaction chamber and other equipment within the reaction chamber. Because electronic devices are so sensitive, even tiny particles from these excess materials can destroy the device during the manufacturing process. Between process steps, the halide gas can be activated by the plasma to react with excess material, thereby removing excess material, such as etching steps throughout the reaction chamber. The most important of these chamber cleaning gases is nitrogen trifluoride (NF3), which is used in almost all electronics manufacturing.
Since humans have been producing electronic devices, gases have been used to implement basic process flows as well as more complex designs and product manufacturing.